The cost of replacing a condenser in a car can vary depending on several factors, including the make and model of the vehicle, the location of the repair shop, and whether you choose to use an original equipment manufacturer (OEM) condenser or an aftermarket one. On average, the cost of a condenser replacement ranges from $400 to $900.
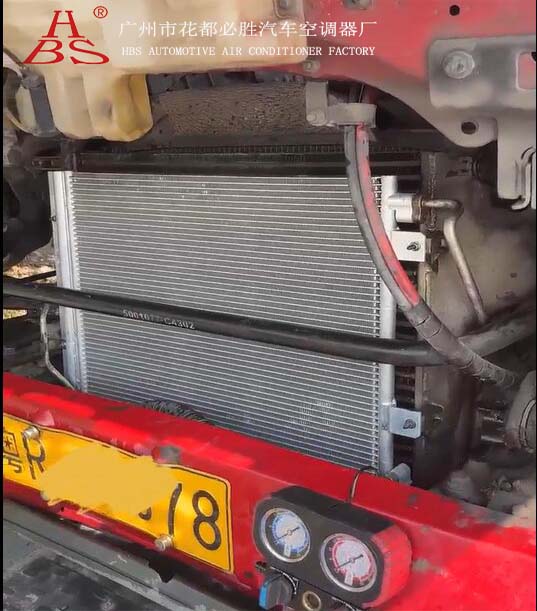
If you take your car to a dealership or an authorized service center, the cost may be higher due to their higher labor rates and the use of OEM parts. However, using OEM parts can ensure compatibility and reliability.
On the other hand, if you opt for an independent auto repair shop, you may find lower prices as they often offer competitive rates and may use aftermarket condensers, which are typically less expensive than OEM parts. Aftermarket condensers can still provide adequate performance but may have slightly different specifications compared to the original.
It's important to note that the cost of the condenser itself is only part of the total replacement cost. Additional costs may include refrigerant recharge, evacuation and recharge of the A/C system, replacement of other components (if damaged), and labor charges.
To get an accurate estimate, it is recommended to contact local repair shops or dealerships and provide them with details about your vehicle. They will be able to provide you with a more precise cost estimate based on your specific circumstances.
To ensure the normal operation of the automotive condenser, regular inspections of its appearance and working condition are necessary. Promptly clean the condenser and check the coolant level and quality. It is important to avoid collisions to prevent damage to the condenser.