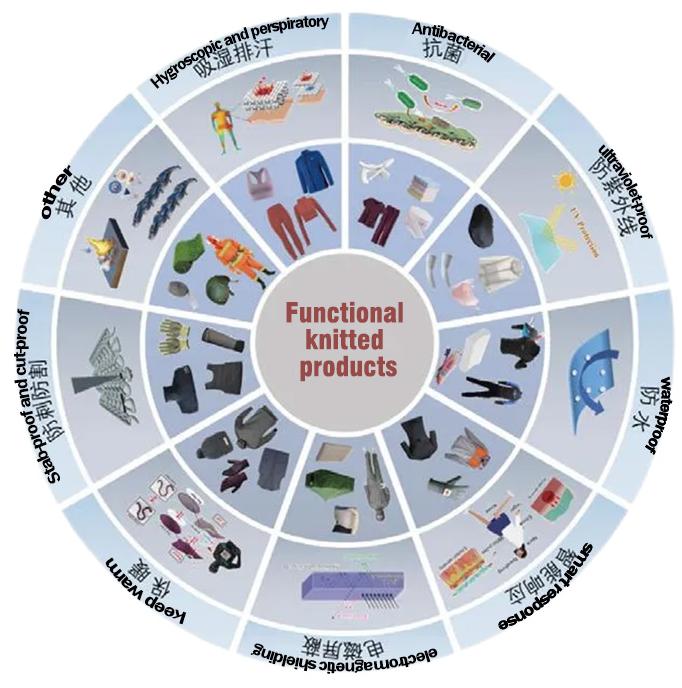
Knitting products are widely used in the three major fields of wear, decoration and industrial use, forming a relatively complete knitting industry chain. Functional knitting products include sports apparel, medical assistance products, military defense supplies & fashion apparel developed through the integration of high-tech material with knitting technology, which not only meet the increasingly diverse needs of people,but also innovate in combination with cutting-edge technology. With the rapid development of science and technology,various functional & diversified products combining traditional textile technology emerge in endless stream. According characteristics of knitted fabrics, functional knitting products, as an important product combining textile technology and scientific innovation, are gradually becoming new focus of the development of the textile industry. At the same time,with the development of green functional knitting products, functional knitwear is not only the result of technological innovation, but also embodiment of market demand and sustainable development trends.
1. Hygroscopic and perspiratory knitted products
The wetting process of sweat involves the contact and penetration between sweat and fiber and fabric surface. The water in this process mainly depends on the capillary action between fiber and yarn to move, and the water finally evaporates rapidly through the fabric surface to achieve the quick-drying effect. Moisture wicking fabric can effectively reduce the retention time of sweat on the skin surface, keep the skin dry and reduce the growth of bacteria, improve the wearer's comfort. Related applications in sports products include cycling clothing, yoga clothing, sports underwear, sports shoes, etc.
2. Antibacterial knitting products
Antibacterial knitted fabrics can realize antibacterial function through five ways: natural antibacterial fiber, regenerative antibacterial fiber, synthetic antibacterial fiber, modified antibacterial fiber and antibacterial agent finishing and processing. On this basis, combined with organizational structure design, product performance can be further optimized and bacterial growth can be effectively inhibited. At present, antibacterial knitting products are used in daily use, medicine and other fields.
3. Uv protection knitted products
Uv protection can be achieved through functional yarns or functional finishing (sunscreen reagents, functional coatings). Anti-ultraviolet function products can effectively block ultraviolet radiation, make the wearer feel more comfortable, extend the service life of the product, in outdoor, use, automotive materials and other fields have been developed and applied.
4. Waterproof knitting products
Waterproof knitted products are made by functional yarn or special finishing technology, which can effectively prevent water from penetrating into the interior of knitted products, prevent stains, fading and fabric deformation caused by water, and improve the durability and quality stability of products. At present, waterproof functional knitting products are used in outdoor sports, daily protection and other fields.
5. Electromagnetic shielding knitting products
Electromagnetic shielding knitting products are used in daily use, military defense and other scenarios. Electromagnetic shielding fabric is an excellent shielding material made of functional yarn with both light weight, flexibility and strength. It is widely used because of its thin and light, good surface adhesion and a large number of grid structures. At present, the design principle of electromagnetic shielding fabrics is mainly to use the conductivity of the material to metalize the surface of the fabric to form a metal conductive layer, or to make conductive filament and conductive yarn first, and then weave into the fabric, so that the metal conductive grid is formed inside the fabric.
6, Smart responsive knitting products
Intelligent response technology provides more possibilities for the development of functional knitting products, in addition to the traditional clothing field, intelligent response knitting products can also be applied to medical, sports, military and other fields. Through intelligent components, knitting products can achieve a variety of functions such as health monitoring, position tracking, and temperature regulation.
7. Warm knitting products
Warm knitting products can be used to form a static air layer inside the fabric through the selection of functional fibers or yarns with warmth, combined with the tissue design, to reduce heat loss, and can also be adjusted by the weaving process parameters (such as density, thickness, etc.) to improve the thermal performance of the fabric. A wide range of warm knit products, including warm underwear, warm coats, warm knee pads and so on. The composite fiber prepared by special process not only makes up for some performance shortcomings of natural fiber, but also shows superior thermal performance. The knitted products prepared by it can also have other properties, such as antibacterial, antistatic, breathable and so on, while having warmth.
8. Stab-proof and cut-proof knitting products
Stab-proof and cut-proof products are widely used in military, medical, sports and other fields, including anti-cut neck guard, stab-proof clothing, stab-proof vest, cut-proof gloves and other products. Among them, flexible stab-proof clothing can not only meet the requirements of special occupations for protective performance, but also suitable for daily wear because of its comfort, which is a research hotspot in recent years. Bulletproof textiles made from high-strength fibers such as ultra-high molecular weight polyethylene (UHMWPE) or aramid provide some protection against projectiles such as shrapnel and ammunition fragments. The traditional full overlay design limits the energy absorption of the composite during ballistic impact. In contrast, the checkerboard design formed by polycarbonate (PC) film and aramid can effectively improve the ballistic performance. The bullet-proof performance of the checkerboard PC film also increases with the increase of the number of spacer layers.
9. Other functional knitting products
Other functional knitting products also include fire retardant, anti-static, anti-mosquito and other products. Among them, the development of antistatic knitting products mainly involves material selection, fabric structure design, application of antistatic finishing technology and many other aspects.
Wuxi Shin Tong Yunn Machinery Technology Co., Ltd fabric dyeing machine DD636 high temperature long tube jet fabric dyeing machine and DD636B series is suitable for dyeing conventional knitted fabrics and functional technology knitted fabrics. Welcome to visit our factory and show the knitted fabric dyeing machine for you.