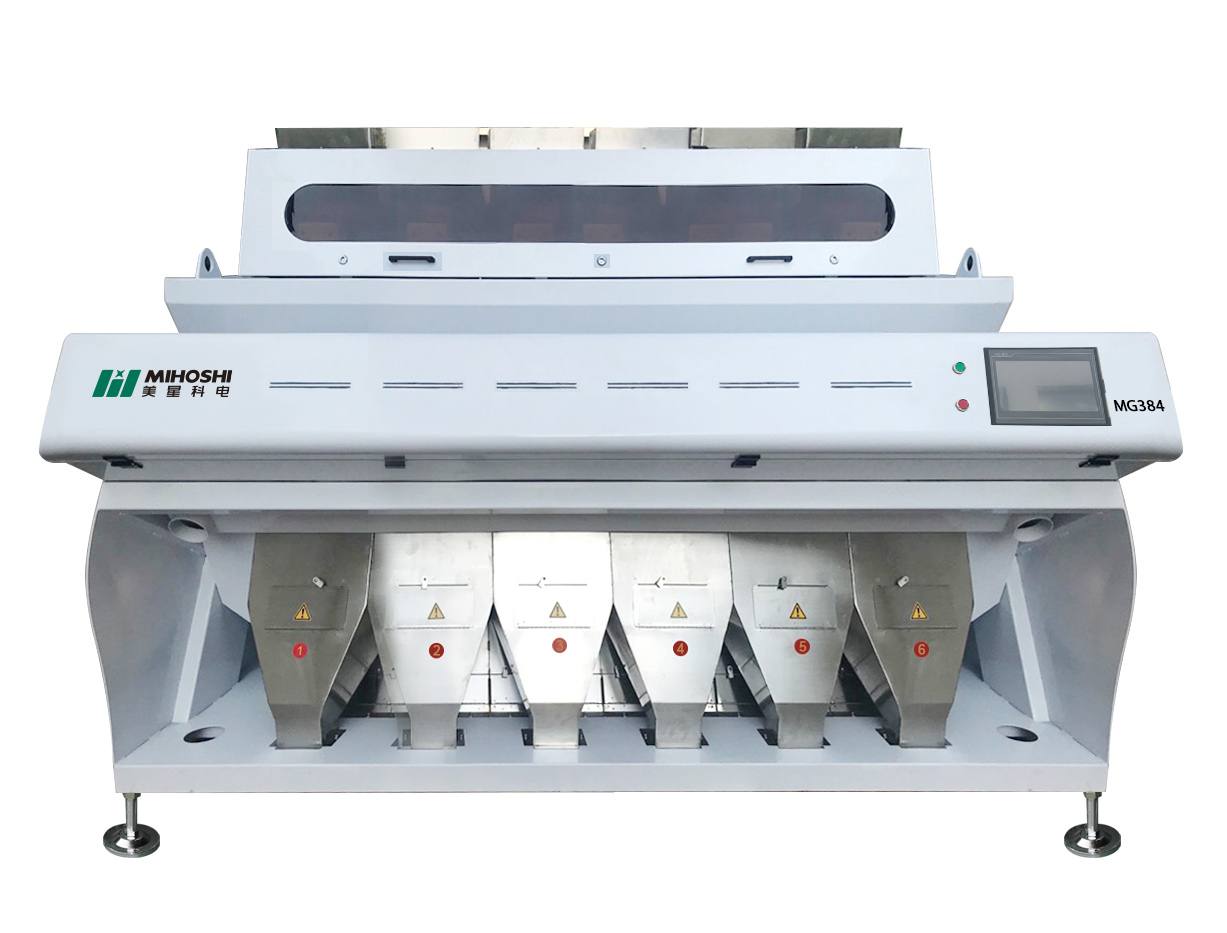
In modern agricultural production, harvesting and processing of grains are important links. In order to improve efficiency and quality, grain color sorter has become one of the indispensable equipment. As a well-known agricultural industrial machinery manufacturer, Mihoshi brand provides a series of efficient and intelligent grain color sorting machines for production and processing companies with its advanced technology and excellent quality. This article will introduce the characteristics and advantages of Mihoshi Valley's selection machine, helping readers choose the equipment that suits their needs.
Characteristics of Mihoshi Valley's Machine Selection
The Mihoshi grain sorting machine adopts advanced optical sensing technology and image processing algorithms, which can comprehensively and accurately sort grains. Its main features include:
Efficient and energy-saving: The Mihoshi Valley selection machine adopts an optimized operating system and an efficient exhaust system to reduce energy consumption and improve work efficiency.
Accurate sorting: The grain color sorter can accurately separate impurities, defective grains, and diseased grains based on their size, shape, color, and other characteristics, ensuring excellent grain quality.
Intelligent control: The grain color sorter is equipped with an advanced intelligent control system, which can adapt to different grain varieties and processing requirements through real-time monitoring and automatic adjustment, providing the best color sorting effect.
Enhanced durability: The Mihoshi Valley selection machine adopts high-quality materials and precise processing technology, with high durability and stability, and can operate stably for a long time.
Mihoshi Valley's advantages in searching and selecting machines
The advantages of choosing Mihoshi Valley for machine selection are as follows:
Reliable Quality: As a well-known brand in the agricultural machinery industry, Mihoshi has always focused on product quality and technological innovation. Choosing the Mihoshi Valley sorting machine allows you to use it with confidence and achieve excellent sorting results. Mihosh
Widely applicable: Mihoshi grain color sorter can be used for sorting various grains, including wheat, rice, corn, etc. It has a wide range of applications and can meet the needs of different crops.
User friendly: The Mihoshi grain color sorter has a simple and easy to understand operating interface and user-friendly design, making it easy for even users without professional knowledge to operate and improve work efficiency.
Customer Service: Mihoshi provides comprehensive pre-sales consultation and after-sales service, including equipment installation, maintenance, etc., to ensure that users receive timely support and assistance during the purchase and use process.
Mihoshi grain color sorter, with its advanced technology and excellent quality, has become an important tool for production and processing companies to improve production efficiency and ensure grain quality. When choosing a grain color sorter, you can consider the Mihoshi brand products produced by Meixing Intelligent Technology Company, and choose the appropriate model and configuration according to your own needs to improve the quality and efficiency of agricultural production.